Comprehending What is Porosity in Welding: Reasons and Solutions
Comprehending What is Porosity in Welding: Reasons and Solutions
Blog Article
Porosity in Welding: Identifying Common Issues and Implementing Best Practices for Prevention
Porosity in welding is a prevalent issue that usually goes undetected until it creates significant issues with the integrity of welds. In this discussion, we will certainly check out the vital elements adding to porosity formation, examine its destructive results on weld performance, and go over the ideal techniques that can be embraced to reduce porosity occurrence in welding procedures.
Common Sources Of Porosity

Utilizing unclean or wet filler products can present impurities right into the weld, adding to porosity concerns. To reduce these usual reasons of porosity, comprehensive cleansing of base steels, correct shielding gas choice, and adherence to ideal welding criteria are vital practices in attaining top quality, porosity-free welds.
Influence of Porosity on Weld Top Quality

The existence of porosity in welding can significantly jeopardize the structural stability and mechanical residential properties of welded joints. Porosity creates voids within the weld metal, weakening its overall strength and load-bearing ability. These gaps serve as tension concentration factors, making the weld extra susceptible to fracturing and failing under applied tons. In addition, porosity can lower the weld's resistance to rust and other ecological aspects, even more diminishing its long life and performance.
Welds with high porosity levels have a tendency to exhibit lower influence toughness and minimized ability to deform plastically before fracturing. Porosity can hamper the weld's capacity to properly send forces, leading to premature weld failing and possible security risks in crucial structures.
Ideal Practices for Porosity Avoidance
To improve the structural honesty and why not try these out high quality of bonded joints, what particular steps can be implemented to reduce the incident of porosity during the welding procedure? Making use of the proper welding method for the specific product being welded, such as adjusting the welding angle and weapon placement, can additionally prevent porosity. Regular evaluation of welds and instant remediation of any type of problems determined throughout the welding procedure are necessary techniques to avoid porosity and generate top quality welds.
Value of Correct Welding Strategies
Executing proper welding techniques is critical in guaranteeing the structural stability and top quality useful site of bonded joints, developing upon the foundation of efficient porosity prevention steps. Excessive warmth can lead to increased porosity due to the entrapment of gases in the weld pool. Additionally, making use of the ideal welding criteria, such as voltage, existing, and travel speed, is crucial for achieving audio welds with very little porosity.
Furthermore, the option of welding procedure, whether it be MIG, TIG, or stick welding, ought to line up with the particular requirements of the task to make sure optimum results. Appropriate cleansing and preparation of the base metal, as well as picking the ideal filler material, are also crucial elements of competent welding techniques. By sticking to these best techniques, welders can reduce the danger of porosity development and generate top notch, structurally sound welds.
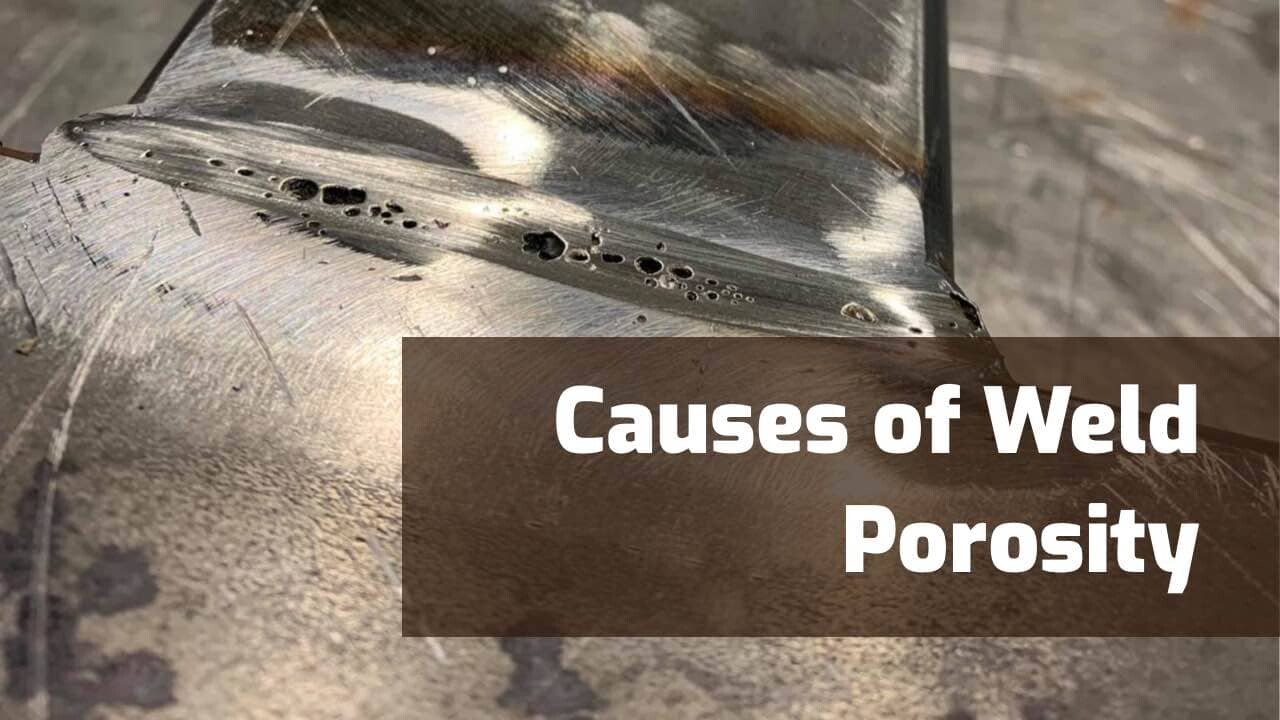
Evaluating and Quality Control Measures
Checking procedures are necessary to detect and stop porosity in her response welding, ensuring the strength and sturdiness of the final product. Non-destructive screening approaches such as ultrasonic testing, radiographic screening, and visual assessment are generally employed to determine possible defects like porosity.
Post-weld assessments, on the other hand, examine the final weld for any kind of issues, including porosity, and validate that it meets specified standards. Carrying out a comprehensive high quality control strategy that includes thorough testing procedures and inspections is critical to minimizing porosity concerns and ensuring the total quality of bonded joints.
Verdict
To conclude, porosity in welding can be a common concern that influences the top quality of welds. By determining the usual root causes of porosity and executing ideal practices for avoidance, such as appropriate welding techniques and screening measures, welders can make sure high top quality and reliable welds. It is vital to prioritize prevention methods to decrease the incident of porosity and keep the integrity of welded frameworks.
Report this page